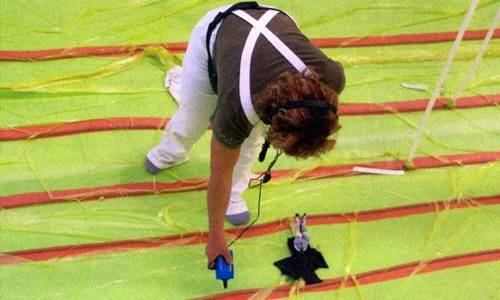
Laminados de
fibra inteligentes, resinas y composites que se curan ellos solos
después de un impacto, así serán los componentes de fabricación de
los barcos en un futuro cercano. De hecho ya se han producido
laminados que cambian de color y se colorean indicando la zona que
ha sufrido tensiones y roturas tras un impacto o un esfuerzo
exagerado. Gracias a este indicador, es posible reparar la zona con
la máxima confianza, asegurando que el casco vuelve a adquirir la
solidez estructural con la que fue concebido.
Incluso será
posible fabricar materiales que se reparen a sí mismos. La
supervisión de la salud estructural puede implementarse mediante
matrices de sensores laminados en el casco que ofrecerán información
de fuerzas y tensiones de las cargas producidas en la estructura. Ed
Findon ingeniero en composites de un importante astillero del
Reino Unido asegura que en unos 10 años tendremos cascos con estas
características. Ya han implementado esta tecnología en el palo del
Mirabella V el velero Sloop más grande del mundo.
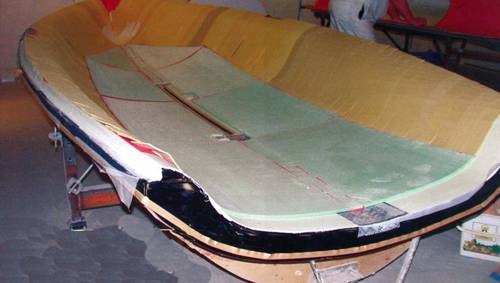
El otro gran
avance se va a producir gracias a los robots industriales. Son
grandes máquinas industriales que mediante tecnología digital y
ordenadores pueden hacer cortes de enorme exactitud en todo tipo de
materiales y tejidos de fibras. Estas piezas son posteriormente
utilizadas para construir el casco y la cubierta mediante una
realización con preimpregnados y con infusión de resinas al vacío.
De esta manera se gana en solidez estructural, en ahorro de peso del
barco y por tanto en una gran mejora en las prestaciones de la
embarcación. Pero resulta igualmente asombroso el enorme ahorro de
tiempo y mano de obra, o lo que es lo mismo de coste en la
construcción. Por ejemplo, para la fabricación de un casco en el que
normalmente emplearíamos unas 300 horas, con los robots pasaríamos a
emplear solo 13 horas! Y la precisión obtenida es total y del orden
de un milímetro, terriblemente mayor a la del mejor operario dotado
de un par de tijeras.
En los
próximos 5 años se van a empezar a utilizar nuevas tecnologías que
mejorarán la calidad y abaratarán los costes de producción de forma
importante. Moldes cerrados que ya se empiezan a utilizar, será la
forma estándar de crear cascos y demás piezas de fibra. El modelado
3D y las fresadoras y máquinas de corte numéricas controladas por
ordenador serán de uso común en todos los astilleros, lográndose
costes de unos 600 € por metros cuadrado de pieza finalizada
totalmente acabada.
Pero quizás
sea más revolucionario la producción mediante termoplásticos como el
poliuretano en barcos de hasta 9 metros de eslora. El resultado será
una producción más económica y con menores daños al medio ambiente y
que además podrán ser reciclados de forma muy sencilla. El sistema
inyecta el plástico en un molde cerrado del que sale la pieza
perfectamente acabada y lista para el mecanizado en una rápida y
sencilla operación industrial. Este sistema de construcción podría
evolucionar a su vez para conseguir aumentar algo más la eslora
máxima admitida por este procedimiento, mediante refuerzos
estructurales en otros materiales introducidos previamente en el
molde antes de proceder a la inyección del termoplástico. Los barcos
que han finalizado su ciclo útil de vida serán fácilmente
reciclables como se hace actualmente con muchas piezas en el mercado
del reciclado de los plásticos.
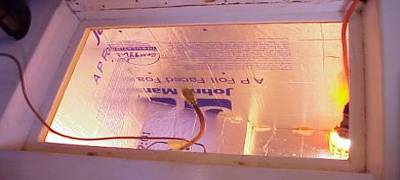
El mercado en
el moldeado de cascos vendrá guiado por las necesidades de cumplir
las normas medioambientales de mejora de salud de los operarios y de
seguridad en la manipulación. Así mismo, la creación de otras piezas
para los barcos como son las bitácoras, tapas, cierres, contramoldes,
guarnecidos interiores y demás elementos empleados en la
fabricación, serán realizados mediante moldes cerrados que
trabajan por inyección produciendo resultados perfectos y a costes
inferiores.
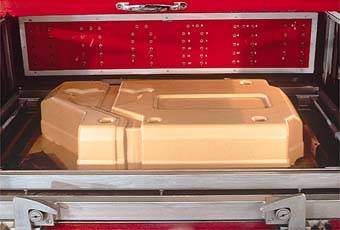
Artículos relacionados:
-
El Acero Inoxidable
-
Materiales y Cascos
oceánicos
-
Ventajas del aluminio
-
Veleros en Aluminio
-
Fibras más fuertes que el acero
|