|
|
|
Volver Menú Infonautic |
|
|
|
¿Cómo funciona la
dirección hidráulica?
|
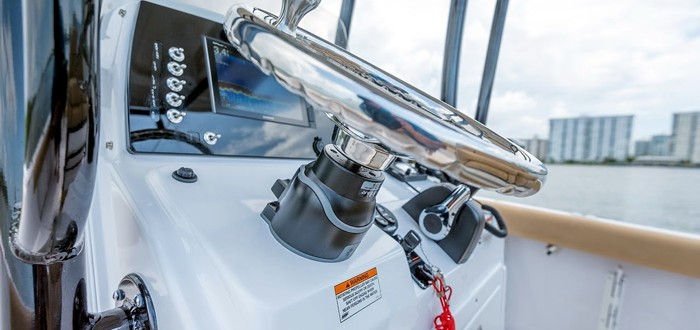
Si tu barco lleva dirección hidráulica, o quieres instalar una, es
importante saber cómo funciona para poder sacar el máximo
partido o resolver cualquier
incidente en la mar.
Conocerlas, da seguridad y nos permitirá poner remedio o mejorar
sistemas demasiado duros o ruidosos.
¿Quieres diseñarte tu propio sistema hidráulico? |
Muchos barcos utilizan sistemas
hidráulicos para mover el timón, especialmente a partir de
cierta eslora, o de cierto desplazamiento, cuando es importante
generar una fuerza significativa en la pala del timón. En
motoras es normal encontrarnos con sistemas hidráulicos a partir
de los 10
|
metros de
eslora, y en veleros por encima de los 50 pies. Pero la mayoría
de los barcos con motorización fuera-bordas, desde pequeñas potencias,
utilizan también direcciones hidráulicas. Al final, siempre
encontraremos un pistón hidráulico, también llamado "actuador",
que es el que mueve el motor fueraborda, o el timón al empujar
una biela o un brazo fijado al eje del timón.
El
pistón hidráulico ‘Actuador’
Este
elemento es el que realmente hace el trabajo duro, moviendo el timón
o el motor fueraborda. Se trata de un émbolo que puede moverse
dentro de un cilindro por el que introducimos aceite a presión
desde uno de los dos extremos. Este aceite, a una presión de unos 30
a 60 bares, proviene de una bomba que activamos al girar el volante.
El mecanismo es muy sencillo, pero su dimensionamiento, aunque es tarea
sencilla, debe ser bien calculado si no queremos tener un volante
demasiado duro, o con el que necesitemos dar demasiadas vueltas para
conseguir el giro de la dirección.
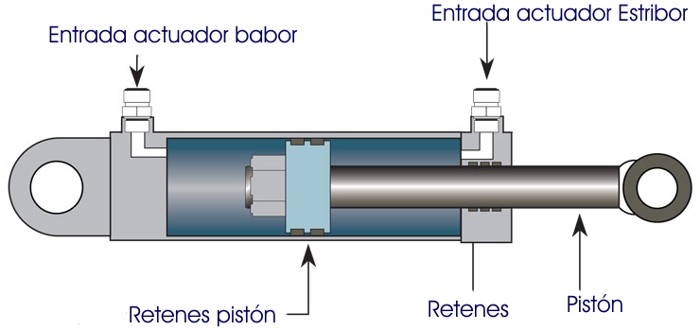
Dependiendo del lado
por el que entre el fluido hidráulico a presión, el embolo se
desplazará a uno u otro lado. La fuerza que ejerce el embolo
dependerá de la presión del aceite y de la superficie del pistón.
Es
interesante observar que en un sistema hidráulico, cuando el timón
está parado, sea cual sea su posición, tanto el pistón como los
tubos hidráulicos continúan a alta presión, para así soportar las
fuerzas a las que esté sometido el timón o el motor fueraborda.
Incluso
una pequeña bomba en el eje del volante de dirección puede hacer
girar un timón muy grande y que ofrezca mucha resistencia, si damos
las suficientes vueltas a la rueda para conseguir realizar el
trabajo necesario. Pero sería muy poco apropiado tener que dar, por
ejemplo, 20 vueltas al timón para conseguir mover el timón de lado a
lado ("lock-to-lock" en la jerga anglosajona). Por ello es
importante saber qué factores intervienen en esta relación y cómo se
puede modificar o diseñar estos tipos de sistemas de dirección.
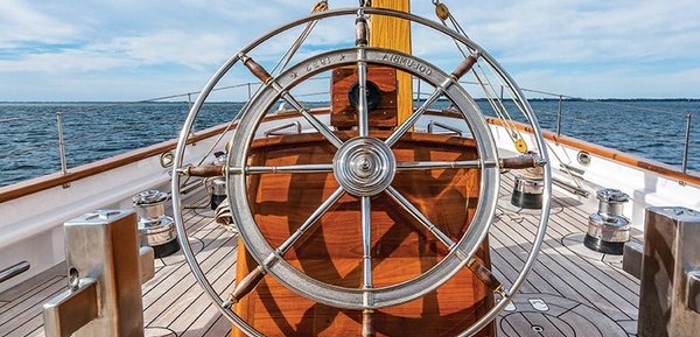
En veleros de gran
eslora en vez de guardines, se suele también utilizar sistemas hidráulicos para mover la
pala del timón.
Existen
barcos en los que por el contrario, el timón se mueve con pocas
vueltas pero está muy duro. Como veremos, también puede
estar duro, aunque giremos bastantes vueltas, debido a otros problema
que explicaremos más adelante.
Las
medidas del Actuador
La
dimensiones del pistón actuador son muy importantes, pues nos
permitirán calcular el número de vueltas a dar en el volante para
conseguir un movimiento completo de la pala del timón o del motor
fueraborda.
Lo
importante es el desplazamiento que indica el volumen interno de
aceite que puede ser desplazado al hacer el movimiento lineal
completo y que, cómo no podía ser de otra manera, es el producto de
la sección del cilindro por la longitud del movimiento del pistón.
El
diámetro de los pistones suele ser medido en pulgadas y los hay de 1,25, 1,50, 1,75
o 2 pulgadas y el movimiento del pistón también en pulgadas suele
ser de 7, de 9 o más pulgadas. Pero también encontraremos estas
medidas en métrica y en centímetros lo cual nos simplificará el
cálculo (al menos a los Europeos).
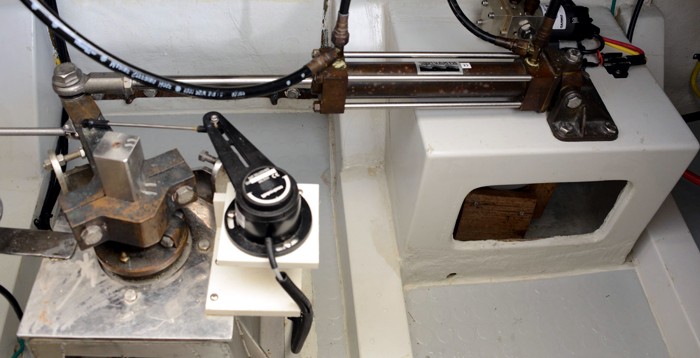
El pistón actuador de
color negro se encuentra en la parte superior de la foto. En el centro aparece de color negro el medidor de ángulo del timón que lleva en su eje un
potenciómetro para pasar esta medida al piloto automático y poder
gobernar dependiendo de las reacciones que tenga el timón.
Si por
ejemplo tenemos un pistón de 5 centímetros cuadrados de sección y hace un movimiento de
15 centímetros lineales (desde máxima extensión a su máxima retracción), su
desplazamiento será de 75 centímetros cúbicos (5x15). Si la bomba del
volante es capaz de mover 15 cc por vuelta, está claro que
necesitaremos 5 vueltas completas para conseguir mover el timón de
lado a lado. Normalmente tendremos que añadir un 10% de vueltas de
volante pues el aceite se "desliza" un poco en la bomba y por tanto
por cada vuelta en realidad estaremos moviendo un poco menos de esos
15 centímetros cúbicos.
La
bomba estática
Lo que
hay detrás del volante de dirección o gobierno, es una bomba que
impulsa el aceite en una u otra dirección al mover el volante. En
muchos barcos esta bomba es manual, es decir, que somos nosotros con
nuestros esfuerzo los que movemos la bomba y por tanto forzamos la
circulación de aceite en uno u otro sentido.
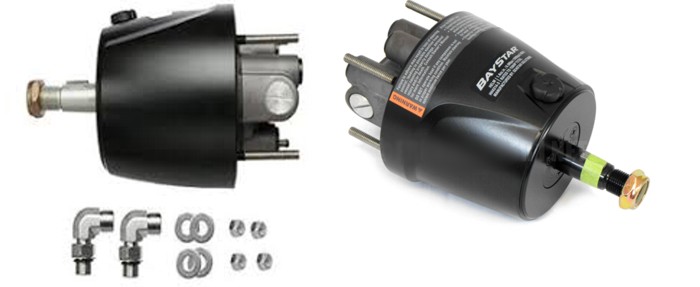
Pero en
barcos de gran tonelaje o con timones muy grandes, necesitamos
asistencia mecánica o electromecánica. La mayoría de los montajes
pasivos sin asistencia eléctrica o mecánica, están diseñados para
tener que dar entre 5 y 10 vueltas completas de volante para mover todo el
timón de banda a banda.
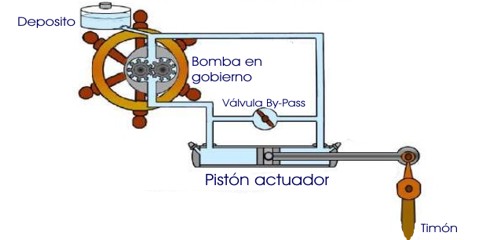
En este esquema de
gobierno hidráulico no asistido, son nuestro brazos quienes mueven
la bomba situada en la rueda de gobierno. Así bombeamos aceite hacia
el actuador que se encarga de mover el timón. Si abrimos la llave de
by-pass el aceite puede fluir libremente sin presión, anulando
el sistema de gobierno hidráulico, pero permitiendo utilizar por
ejemplo una caña de respeto conectada directamente al tintero del
timón. Necesario por ejemplo, si se estropeara la bomba o si
tuviéramos una rotura o pérdida importante de fluido hidráulico en un manguito...
Cómo
calcular el ratio de giro
La
mayoría de los timones se mueven 35º a cada banda o lo que es lo
mismo un total de 70º, aunque algunos timones en embarcaciones
lentas con grandes necesidades de maniobra portuaria lo hacen en 45º
a cada banda. Si por ejemplo tenemos un desplazamiento de 8 vueltas
de volante (360º por vuelta) y lo dividimos por los 70º del timón,
obtendremos el ratio de giro, en nuestro ejemplo (8x360/70) de
aproximadamente 41:1, es decir, que por cada grado de giro del
timón, habremos de girar el volante 41 grados.
Cómo
funciona la bomba de la rueda
Encontraremos proveedores italianos, franceses, norteamericanos o
incluso Koreanos. Marcas como Capilano, Hynautic, Jastram,
Vetus, Teleflex, Twin-Disk o SeaFirst.
Naturalmente cada fabricante propone diferentes prestaciones y
calidades, pero muchos están fabricados según un esquema bastante
parecido, consistente en una serie de pistones distribuidos
radialmente. Los pistoncitos son empujados por un disco que gira
cuando movemos el volante con un determinado ángulo respecto al eje
de giro. Al moverse, el disco va empujando uno atrás otro cada uno
de estos pistoncitos radiales.
Algunas bombas permiten ajustar el ángulo de este disco, lo que hace
que aumente o disminuya el volumen de aceite impulsado por cada
vuelta, o lo que es lo mismo, permite ajustar el desplazamiento de
la bomba y por tanto la dureza del volante, haciéndolo más suave a
cambio de necesitar más vueltas de volante para conseguir el
movimiento de la pala, o viceversa.
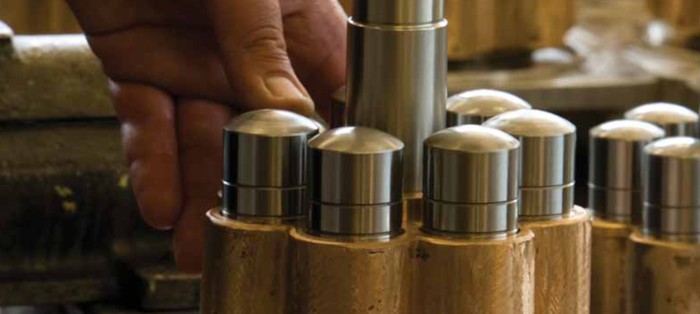
Pistones de una bomba
de dirección. Al girar la rueda, empujamos uno tras otro cada uno de
estos pistones que impulsan el liquido hidráulico, del mismo modo
que lo hace una jeringuilla de inyecciones.
Otros
fabricantes montan un sistema de rueda de excéntrica que permite
presurizar el aceite que es guiado en una u otra dirección
dependiendo el movimiento de unas válvulas desplazadas al comenzar a
mover el volante en una u otra dirección.
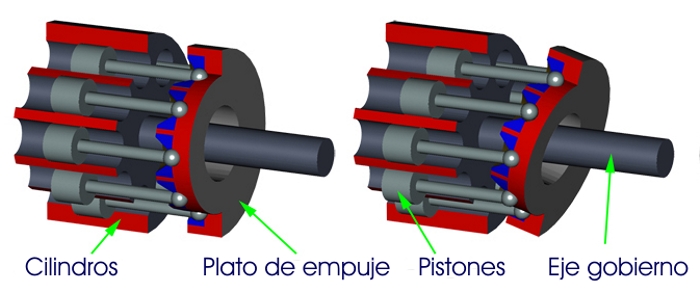
Existen bastantes
tipos de bombas hidráulicas, y este es uno de ellos bastante
utilizado. Cuanto mayor sea el ángulo del plato, mayor será el
desplazamiento de cada pistón, por tanto más aceite desplazará la
bomba pero más fuerza tendremos que hacer al volante. En algunas
bombas, el ángulo se puede ajustar para cambiar el
comportamiento de la dirección.
Sea
como fuere el sistema utilizado, lo importante es entender que el
aceite solo puede circular en una dirección definida por el timonel
al mover el volante, y no puede retornar, o lo que es lo mismo, la
bomba no se puede comportar como un "motor" si la inyectáramos
aceite a alta presión en dirección contraria. Esto es importante,
pues si tenemos dos puestos de gobierno, uno en el interior del
barco y otro en el fly-bridge, al mover una de las dos ruedas de
gobierno,
queremos que la presión de aceite haga mover el actuador, y no hacer
girar la otra rueda de gobierno. Y lo mismo ocurre con una tercera
bomba que puede ser eléctrica para poner en marcha el sistema de
piloto automático.
Dos
líneas o tres líneas
Muchas
instalaciones hidráulicas son evidentes, al existir solo dos tubos
que salen de la bomba del puesto de gobierno y que van a parar al actuador. Sencillo y lógico.
Pero en
instalaciones con dos volantes de gobierno, existe un tercer tubo de
sangrado que se une a las dos unidades de control, e incluso van
también a la bomba eléctrica del piloto automático.
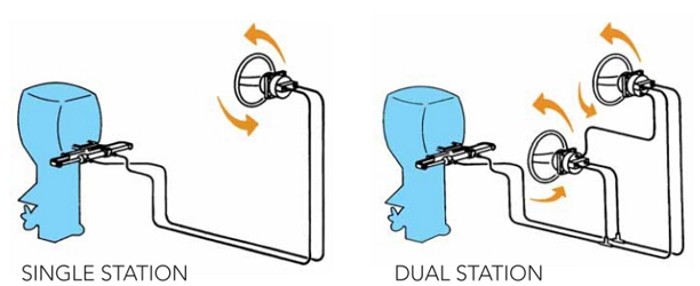
Por
ejemplo, el fabricante norteamericano Tele-Flex e Hynautic (que
ahora también pertenece a Tele-Flex), tiene el tercer tubo –central- que es
utilizado para interconectar diferentes bombas de gobierno y hacer
más sencillo las operaciones de purgado y sangrado, aunque una de
ellas esté a varios metros por encima, por ejemplo en el Fly-bridge
del barco. En otros fabricantes, esta tercera línea queda conectada
a un depósito de aceite hidráulico que mantiene el sistema siempre
en el estado de purga correcta.
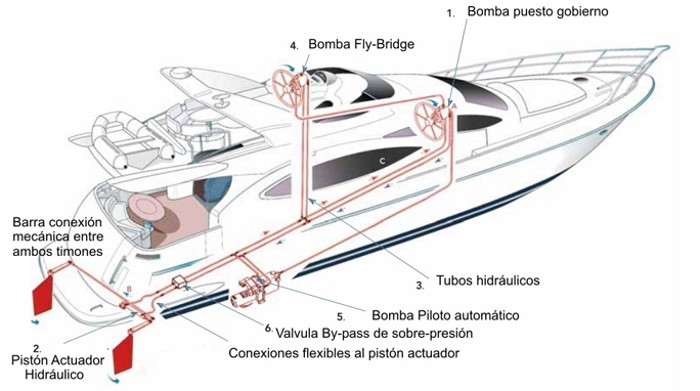
Dureza en la dirección
El
aceite es viscoso y por tanto ofrece rozamiento y fricción en el
interior del sistema hidráulico. Si a pesar de tener una correcta
relación de varias vueltas de volante, este está demasiado duro, es
posible que tenga demasiadas pérdidas debidas a la fricción
hidrodinámica en el interior de los tubos. Cuantos más codos, ‘T’ y
empalmes, más rozamiento y mayor esfuerzo en el volante. Otra causa
típica de dureza en la dirección se debe al empleo de tubos hidráulicos demasiado finos lo que
obliga a una velocidad alta del fluido hidráulico en el sistema, lo
que a su vez aumenta la fricción y la dureza. A mayor diámetro de
las tuberías menor velocidad del fluido hidráulico, y por tanto más
suavidad en el volante.
La
viscosidad también es importante, pues si utilizamos un líquido
demasiado viscoso dentro del sistema, notaremos un aumento en la
dureza de la dirección debido a las pérdidas por rozamiento en
líquido en las pareces del circuito hidráulico.
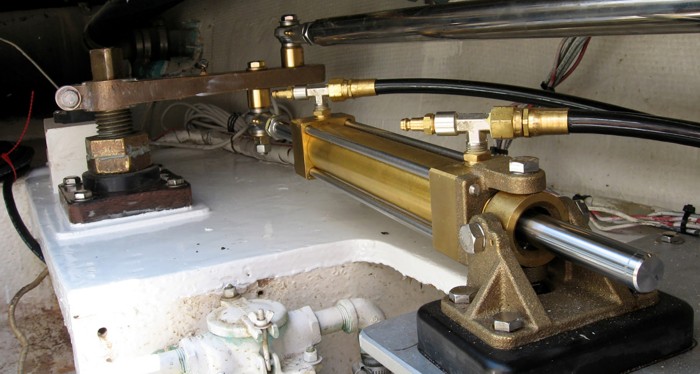
El soporte en donde va
fijado el actuador, debe ser muy sólido pues por reacción habrá de
soportar toda la fuerza que ejerce la pala del timón. Vemos como el
soporte del cilindro en bronce, está montado en un cardán que
permite el movimiento del actuador pues dependiendo de la posición
del brazo, el ángulo del actuador varía ligeramente.
Al
diseñar el sistema de tuberías en la hidráulica de nuestro barco,
debemos reducir en lo posible los ángulos de 90º y los codos
demasiado forzados. En cuanto al diámetro de la tubería, para bombas
de entre 25 cc hasta 50 cc de desplazamiento por vuelta debemos
utilizar tubería de entre 5/16’’ y 3/8’’. Si la bomba es más
potente, de 50cc a 100cc por vuelta, debemos sin lugar a dudas
saltar a un diámetro de tubo de ½ pulgada. La opción de utilizar
tubo de cobre de calidad, normalmente utilizado para instalaciones de refrigeración, es
adecuado pero en las ‘T’ y uniones con maguitos o lo que necesitemos
conectar, debemos utilizar soldadura estaño/plata que tiene una
dureza mucho mayor al típico estaño/plomo. Para ello no basta la
temperatura de soldadura del soplete típico de fontanería, y debemos
soldar con más calor con soldador de mezcla de gases con oxígeno.
Si a
pesar de todas estas cuestiones su dirección va demasiado dura,
debemos investigar si la náutica que la instaló hizo un buen diseño.
En una Motora de 8 metros de eslora y motorizada con un fueraborda
pesado de 350 caballos la dirección estaba demasiado dura y todo
parecía en buen estado con un correcto montaje. El problema radicaba
en que solo había de dar 3 vueltas para girar el motor de
trescientos kilos de peso de lado a lado. El calculo de
desplazamientos fue mal efectuado y deberían haber escogida una
bomba que desplazara la mitad de aceite en cada vuelta, para que
aunque hubiese que dar más vueltas, la fuerza en el volante fuera la
mitad de importante.
Sistemas de gobierno asistidos
A
partir de las 10 o 20 toneladas va siendo normal encontrar barcos
con sistemas hidráulicos asistidos por bombas eléctricas o movidas
por la misma potencia del motor principal. Es decir el timón no se
mueve por la fuerza del patrón por mucha desmultiplicación que sea.
En
estos sistemas el circuito tiene diferentes electroválvulas que son
activadas para ayudar al sistema de gobierno y suplementar la fuerza
que podemos hacer con nuestras manos en la bomba del puesto de
gobierno. En definitiva, se trata de "multiplicar" la fuerza que
podemos ejercer sobre la rueda del timón. La potencia de las bombas
está entre medio caballo y 3 caballos lo cual, aunque pueda parecer
pequeño, en realidad es muy importante si tenemos presente que la
potencia que una persona humana puede ejercer en el volante es del orden de una
veinteava parte de un Caballo de potencia (1/20 CVs).
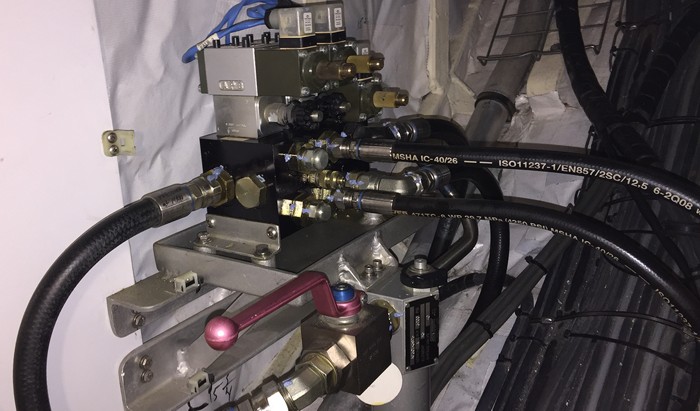
Grupo hidráulico con
varias electro-válvulas situadas en la parte superior de la imagen.
Otra
consideración importante es que hay muchos barcos en el mercado con
asistencia hidráulica de excesiva potencia, por culpa del astillero que no quiere
arriesgarse a quedarse corto. Es un error, pues el exceso de
potencia en el sistema hidráulico de gobierno además de consumir
energía, genera inconvenientes al sobrecalentar el fluido hidráulico
que tiene que circular por el by-pass a mucha velocidad generando
también ruidos agudos molestos en la sala de máquinas.
La
importancia del diámetro de la rueda del timón
Algunos
veleros tiene una rueda del timón desmesuradamente grande, mientras
que algunas motoras llevan un volante muy pequeño. ¿Por qué?
Aunque
todo el mundo lo sepa, hay que recordar que la fuerza del par que
podemos ejercer, es proporcional y mayor cuanto más grande sea el
radio de la rueda. Al final lo que todos queremos es que la rueda
tenga la mejor proporción y estética para nuestro barco. En un
sistema hidráulico asistido, el tamaño no tiene importancia pues
disponemos de fuerza adicional, y por ello los yates con sistema
hidráulico asistidos suelen tener un volante de pequeñas
dimensiones. Por el contrario un velero de regatas que necesita
sensibilidad y poder ejercer fuerza sobre la pala del timón, que casi
siempre es de tipo pasivo y por tanto no tiene asistencia, requiere
una rueda que maximice el par de fuerzas ejercido.
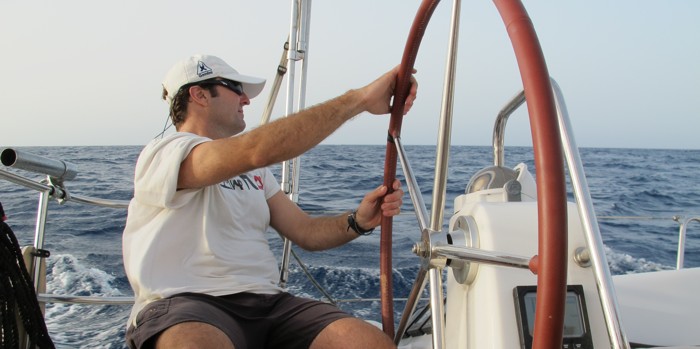
A mayor diámetro de la
rueda, más fuerza o mayor par-de-fuerza, podremos ejercer en el
sistema de gobierno. Por ello en los veleros que no llevan
asistencia mecánica, las ruedas de timón suelen ser grandes,
independientemente de si estas mueven un sistema de guardines o una
bomba de fluido hidráulico.
De la
misma manera que para sacar una tuerca endurecida utilizamos una
llave de mayor tamaño, con la rueda del timón ocurre lo mismo. Cuanto
mayor sea la rueda, menor fuerza necesitaremos para conseguir el
mismo par de giro.
En
sistemas de gobierno hidráulicos pasivos, si no tenemos espacio para
una rueda de mayor tamaño, habremos de incrementar el ratio de
desmultiplicación y por tanto tendremos que dar más vueltas al timón
para conseguir girar todo el timón de lado a lado.
Tubos hidráulicos
En la
canalización del fluido hidráulico debemos utilizar manguitos
hidráulicos de goma reforzados con mallas metálicas para soportar
altas presiones, o tubería de cobre, o de bronce soldada. En motoras
de pequeñas esloras lo normal es encontrar manguitos que van
conectados entre el pistón de la dirección del fueraborda y la bomba
del volante. Pero en yates mayores, también encontramos
distribuciones de hidráulico por tubos soldados. Cerca del actuador,
estas tuberías hidráulicas se conectan a dos manguitos
flexibles por los que continúa el circuito hidráulico hasta el
pistón que mueve el timón.
La IMO
y las normas SAE indican que debemos utilizar manguitos reforzados
con mallas metálicas inoxidables y/o tuberías de cobre capaces de
soportar las altas presiones generadas en bombas y pistones
hidráulicos. Estas pueden alcanzar cifras que dependen del diseño de
la instalación, y que normalmente estarán entre los 15 y los 30
bares de presión, por lo que por seguridad, los circuitos deben poder soportar
presiones de entre 30 y 60 bares.
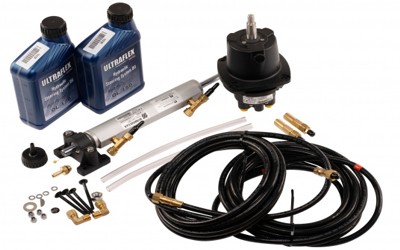
Los tubos por los que
se mueve el fluido hidráulico pueden ser manguitos hidráulicos que
aguantes presiones altas de hasta unas 30 atmósferas o
canalizaciones rígidas en tubo de cobre. La sección de estos tubos
es asunto importante pues si son demasiado estrechas, aumentará
excesivamente la velocidad del fluido hidráulico en su interior.
Si
vamos a montar nosotros mismos el circuito, en las uniones de
manguitos debemos utilizar selladores anaeróbicos y resinas epoxis,
evitando el uso de cinta de teflón como demasiadas veces vemos en
algunos videos de YouTube. Si unos hilos de teflón se cuelan al
interior del sistema, pueden acarrear problemas en las bombas y por
ello debemos evitar su uso.
El
fluido hidráulico no debe ser excesivamente viscoso, y podemos bajar
hasta un ISO-15 para conseguir aún más suavidad.
Direcciones ruidosas
Ya
hemos comentado algunas de las causas de ruidos, al hablar de los problemas con
la dureza de la dirección. Al margen de problemas mecánicos por un
mal funcionamiento de la bomba de la dirección, la causa normal de
los ruidos proviene de un mal diseño y cálculo incorrecto de las
tuberías de distribución hidráulica.
Si el
fabricante ha utilizado tubos algo demasiado finos para ahorrar
costes (lo cual ocurre en bastantes ocasiones) el aceite tiene que circular a más
velocidad y por tanto genera más roce con las paredes del tubo y
crea un
ruido "típico" debido al movimiento hidráulico, cuya única solución es
cambiar la instalación con tubos de mayor diámetro.
Con ello, aunque tengamos que
meter más aceite en el circuito la primera vez, para un mismo
desplazamiento del pistón actuador en una misma unidad de tiempo, la
velocidad del movimiento de este aceite por las tuberías será más
lento, y hará del sistema una dirección más suave y silenciosa.
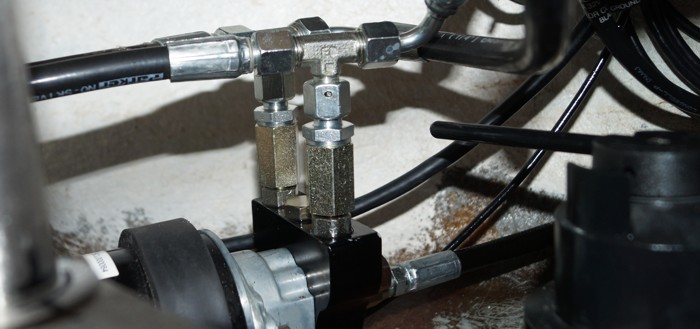
En
sistemas hidráulicos asistidos, es demasiado "normal" montar una
bomba eléctrica que mueve demasiado aceite y por tanto el exceso de
presión debe ser eliminado en una válvula de "by-pass", que está
siempre "pitando" instalada casi siempre en la sala de máquinas,
cerca de la bomba asistida, o del pistón hidráulico.
¿Qué
es la válvula de By-Pass?
Sólo se
suele encontrar en instalaciones hidráulicas que tengan asistencia
mecánica o electromecánica. En estos sistemas, la bomba de aceite,
que en náutica de recreo normalmente suele ser de 0,5 cv, hasta
potencias a 2 ó 3 CV genera presión en el sistema para que siempre
tengamos presión "‘disponible" y lista a ser canalizada al pistón actuador.
Cuando
en navegación no es necesario mover el timón, como ocurre la mayor
parte del tiempo, el exceso de presión generado por la bomba debe
ser "puenteado" para que retorne a la bomba sin que se mueva el
actuador.
Este es
el cometido de la válvula de by-pass. Simplemente es una válvula
tarada a una presión determinada, por encima de la máxima presión admitida en el pistón actuador, que permite recircular el fluido hidráulico por encima de
la presión máxima de trabajo del circuito.
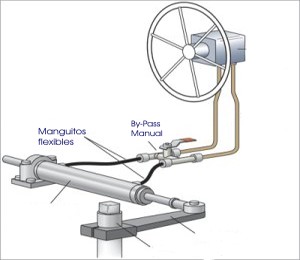
La válvula de By-Pass
puede ser manual para poder desactivar el sistema hidráulico, o
automáticas, taradas a una determinada presión para disiparse
en
una sobre presión, en caso de utilizar un diseño asistido por una
electro-bomba como ocurre en motoras a partir de cierta eslora.
Al
recircular aceite por el By-Pass, ésta hace ruido que se suma al
ruido del aceite al circular por las tuberías.
Este
tipo de instalaciones son sumamente ineficientes, pues el 95% del
tiempo, los 2 ó 3 cv de la bomba se "gastan" en recircular aceite,
hacer ruido por fricción, que finalmente se convierte en calor y
aumento de temperatura en el circuito.
En una
motora de 50 ó 60 pies la potencia de la bomba suele ser de uno o
dos caballos, energía perdida o absorbida de la potencia de
propulsión del motor, sea esta directamente restada por una bomba
hidráulica y mecánica, conectada por una correa, o bien eléctrica desde el
alternador también conectado por su correspondiente correa.
Un
funcionamiento mucho más racional e inteligente tiene lugar en los
sistemas hidráulicos montados normalmente en veleros, en donde la
energía nunca sobra. Así cuando el sistema necesita presión
hidráulica para corregir el timón, y sólo en ese momento, un
presostato dispara el funcionamiento de la bomba hidráulica.
Así es
como funcionan también todos los grupos de presión hidráulica
necesarios para el funcionamiento de pasarelas, elevación de puertas
de garajes, winches hidráulicos, enrolladores de velas… Temas
suficientemente extenso al que dedicaremos otro artículo en
profundidad.
Instalar un pistón hidráulico
Existen
dos puntos importantes a tener en cuenta tras haber calculado y
elegido un actuador que necesitamos en función de la fuerza que este
ha de realizar y el volumen de aceite que debe tener en relación con
la capacidad de la bomba que lo ha de "‘mover", sea esta manual o
asistida por un motor eléctrico o de otro tipo.
El
primer asunto es analizar y definir cuál será el "lugar geométrico"
del movimiento y por tanto tener claro cómo es la geometría del
movimiento que necesitamos. A veces es sencillo, como en el caso de
un timón de gobierno, y a veces muy complicado con sistemas de
bieletas y palancas que pueden lograr movimientos sorprendentemente
curiosos y sofisticados. No es el caso, pero se puede hacer.
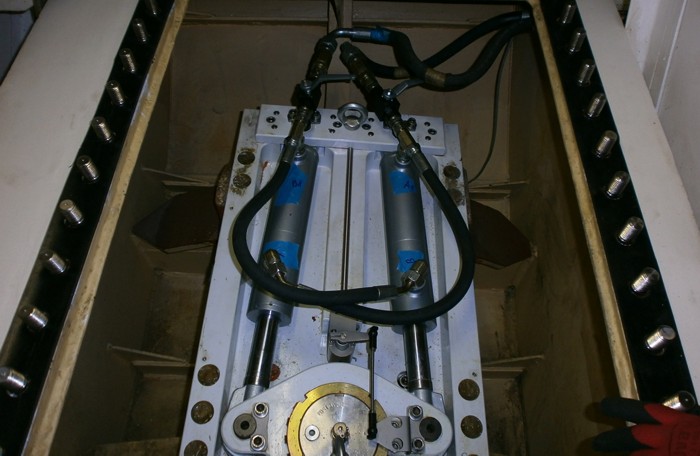
Este montaje utiliza
dos actuadores para mover el eje del timón. Observamos como el
manguito que conduce el aceite en un sentido va conectado a los dos
pistones pero en extremos contrarios a través de una 'T'. De este
modo el fluido hidráulico mueve simultáneamente los dos actuadores
pero en direcciones opuestas.
Debemos
tener presente que ambos extremos de actuador deben poder moverse
libremente en uno o dos ejes de libertar para permitir la elongación
del actuador. Hacer una maqueta en cartón a escala real puede ser
conveniente para asegurar la libertad de movimientos de todos los
componentes, antes de lanzarse manos a la obra.
Las
uniones con bola son cada vez más utilizadas y muy convenientes, al
permitir eliminar el juego normalmente producido por otro tipo de
uniones más tradicionales con un pasador.
Dependiendo de la longitud de la bieleta final que mueve el actuador
podemos modificar el ángulo máximo que puede girar el timón, o la
altura que tenga que subir una puerta de garaje, por ejemplo.
El
segundo asunto consiste en conseguir un montaje físico que sea
suficientemente sólido para poder aguantar los esfuerzos muy
elevados que produce la acción y reacción del pistón hidráulico.
Normalmente estamos limitados al espacio de un tambucho y un mamparo
que no tiene que ser necesariamente demasiado sólido, o un espacio
en el que no encontramos un soporte en el que fijar el actuador.
Debemos
ser creativos y montar una estructura rígida con contrachapado
marino que posiblemente convendrá reforzar laminando con fibra de
vidrio. En otras situaciones podremos encontrar alguna varenga o
viga en la que podemos atornillar un pieza de inox de dimensiones
suficientes, para descargar las fuerzas en distintos puntos y por
tanto aumentar la resistencia a la reacción del pistón.
Si
tiene que atornillar una pieza de aluminio con otra de bronce es
buena idea utilizar entre medias una pieza de nylon,
o polietileno, para que con el tiempo no tengamos disgustos
galvánicos y en un futuro también podamos revisar y desmontar el
conjunto sin
problemas.
Artículos relacionados:
-
Automatiza tu barco; la potencia
electro-hidráulica
|
© Copyright Fondear, S.L.
|
|