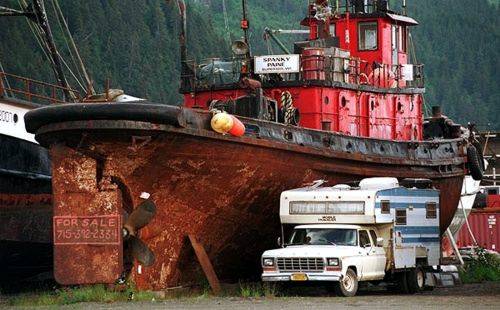
Los cascos metálicos, y sobre todo los de
acero, están sometidos a
esta fatalidad. Para protegernos de ella debemos entenderla. La oxidación es una reacción química natural que
convierte al hierro en sus óxidos más estables. En el mar estos
procesos se aceleran debido al medio salado.
El oxido no es
más que el resultado de una reacción química donde el oxígeno
del aire y el disuelto en el agua de mar se combina con el hierro
para crear óxido férrico. Es natural como la vida misma y ocurre
irremediablemente al buscar el hierro su estado más estable en forma
de oxido de hierro combinado con el oxígeno.
La capa de oxido
que se forma aísla al acero del casco que queda debajo, deteniendo
el proceso químico de oxidación hasta que no se vuelva a poner el
acero limpio en contacto de nuevo con el oxígeno. El problema es que
el óxido de hierro se desprende y disuelve fácilmente lo cual deja
al descubierto el nuevo acero para continuar con el proceso
destructivo.
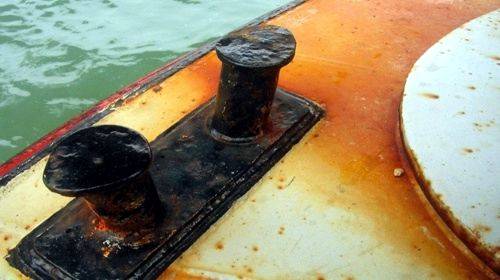
Como la oxidación
se produce en agua salada o ambiente húmedo,
la reacción es mucho más virulenta al producirse un efecto
electroquímico acelerado por la sal disuelta en el agua de mar. Y todavía puede ser peor debido a las corrientes
eléctricas en el casco, producidas por efectos de fricción del
movimiento del barco, o por la utilización de metales diferentes,
que actúan entre sí como si se tratara de una verdadera pila
eléctrica.
La corrosión electroquímica
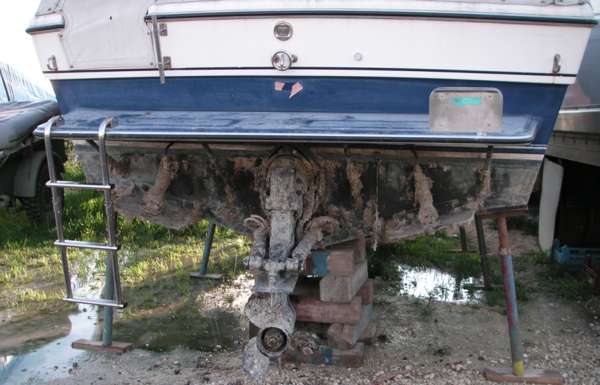
Cada metal tiene
una tendencia diferente a ganar o perder electrones, tendencia
conocida como “potencial electroquimico”. Si ponemos en contacto dos metales de distinto potencial
eléctrico, en contacto directamente o en agua salada
que permite la circulación de la corriente eléctrica, se producirá la corrosión.
Al juntar dos metales, uno
con muchas ganas de perder electrones y otro con muchas ganas de
ganarlos y además los ayudamos por un buen conductor de electrones
como lo es el agua de mar con iones disueltos, lograremos una perfecta corrosión!
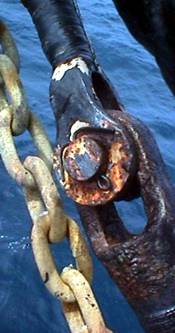
El flujo de estos electrones es lo que llamamos corriente eléctrica
capaz de iluminar las luces de navegación o hacer funcionar los
motores eléctricos.
Es decir en las
pilas de una bombilla hay electricidad porque se oxida un metal
dentro de ellas, a cambio de obtener electrones y por tanto
corriente eléctrica.
A mayor ganas de circular los electrones, mayor voltaje existirá, y
es a esto a lo que se llama potencial electroquímico. Los metales
nobles como el oro o el platino no tienen ninguna gana de perder o
ganar electrones por lo que son perfectamente estables. Cuando un
metal pierde un electrón el hueco que deja es sustituido por un
átomo de oxigeno creando un elemento distinto llamado oxido.
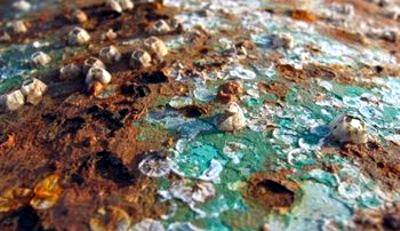
El agua de mar
actúa como electrolito es decir un líquido en el que flotan
cargas eléctricas y capaz
de hacer circular a los electrones libres, vengan de donde vengan, actuando como
un conductor eléctrico.
En los mercantes
se aprecia como la línea de flotación está muy corroída porque el
agua de la superficie está mucho más oxigenada que el resto
facilitando la oxidación. A mayor temperatura más corrosión pues con
la temperatura se facilita la
reacción de oxidación. Si un ácido contamina el agua también aumenta
la corrosión, mientras que en ambientes alcalinos se retarda la
corrosión. Por esta razón se bañan los interiores de los tanques
metálicos con una lechada de cemento que es
alcalino y protege de la oxidación.
La corrosión
galvánica
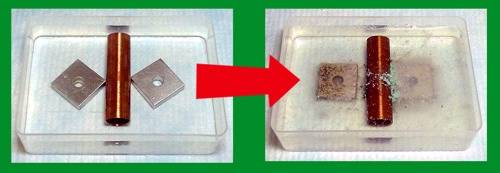
Al ponerse en contacto dos metales diferentes se produce una
corriente eléctrica. El agua salada del mar actúa como conductor de
los electrones que parten del metal que se oxida hacia el metal que
los recibe llamado cátodo. En la imagen los dos ánodos de cinc se
oxidan y disuelven perdiendo electrones y convirtiéndose en oxido de
cinc.
El metal menos
noble se vuelve el ánodo y pierde electrones en el agua del
mar, mientras el metal más noble se vuelve cátodo, adquiere la carga
negativa al atraer a todos los electrones libres. El metal menos noble
se convierte en óxido. Cuando esta reacción continúa, el cátodo se cubre de una
película cedida por las partículas del metal anódico.
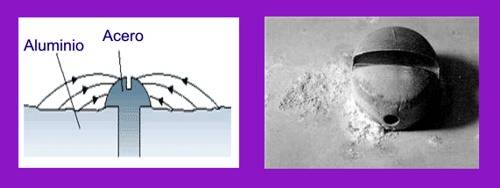
Por esta razón se
puede proteger la chapa de acero con un baño de cinc. Pero si se
ralla la protección desaparecerá. En un casco de acero, no debemos
utilizar antifouling con base de cobre ya que este metal es más noble
y por tanto capaz de oxidar al hierro. El riesgo de corrosión
galvánica es mayor en las zonas del casco sumergidas.
En un barco
utilizamos diferente tipos de metales como son hélices de bronce,
ejes del motor de acero inoxidable, mástiles de aluminio y cables de
conducción eléctrica de cobre. Debemos asegurarnos de que ningún
metal está en contacto con otro distinto y por ello los deberemos
aislarlos entre sí con una pintura adecuada y protegerlos con ánodos de
sacrificio de cinc de buena calidad en las proximidades de los
elementos a proteger. La corrosión galvánica también se produce en
los barcos de fibra creando corrientes la quilla de hierro y la
hélice de bronce o los tornillos y piezas del acastillaje.
Corrosión
electrolítica
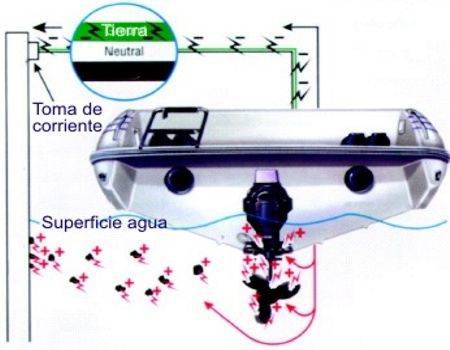
Es la peor de
todas porque puede llegar a ser muy rápida y se produce cuando
existe una corriente eléctrica exterior debido a un
cable eléctrico del circuito del barco caído en la sentina, o por
una conexión mal hecha de la batería, un mal
aislamiento de los cables del barco en contacto con algún metal, o
un mal aislamiento de la toma de corriente del pantalán.
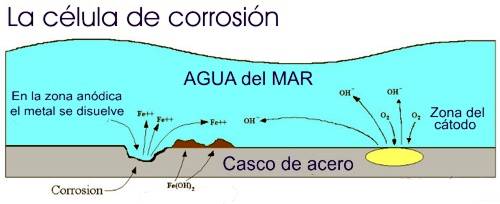
El acero del
casco de un barco es un material homogéneo pero con pequeñas zonas
de diferente potencial eléctrico, que ayudados por una corriente
externa formarán células galvánicas que originarán puntos de
oxidación.
Existen
dispositivos electrónicos denominados “circuitos de corriente
impresa” que miden las pequeñas diferencias de potencial eléctrico
entre las diferentes partes metálicas de los barcos, incluidos los
ánodos de sacrificio, y generan una corriente inversa que anula
estas variaciones de potencial evitando la oxidación. Estos sistemas
detectan las variaciones de voltaje que puedan existir y envían
corrientes ligeramente mayores a determinados ánodos para
neutralizar las zonas en la que se esté produciendo la corrosión.
Los sistemas son delicados y totalmente desaconsejados para cascos
de aluminio.
Los ánodos de sacrificio

Como el cinc es
menos noble que el acero, el cinc se volverá ánodo cediendo
partículas y protegiendo al acero que es mas catódico en la escala.
Se deben colocar
ánodos de cinc cerca de la unión de metales distintos. No se
aconseja colocar ánodos de cinc en zonas de turbulencias. En cascos
de hierro los ánodos de cinc serán conectados eléctricamente al
casco por medio de tornillos soldados directamente sobre el
enchapado del forro. Bajo ninguna situación los ánodos de sacrificio
pueden ser pintados, pues esto los aislaría deteniendo el proceso
migratorio de cinc hacia el acero del casco y por tanto la
protección. El magnesio está aún mas abajo que el cinc en la escala
galvánica y se puede utilizar como material para ánodos,
pero er
mucho más caro.
Existe una fórmula utilizada para calcular el peso total de los ánodos de sacrificio que son necesarios instalar en
barcos que navegan permanentemente en agua de mar y que viene dada
por la expresión.
Peso = K .
L
( B + 2.D ) / 15,6
El Peso (en
libras) dependerá de L que es la eslora total de flotación en pies, B es la manga también en pies,
D es el calado en pies y K es un
coeficiente que valdrá 0,165 para cascos de fibra de vidrio 1.0 para
barcos de acero y 0,625 para cascos de aluminio.
Para un velero de
40 pies de fibra la fórmula aconseja unos generosos 4 kilos de
ánodos de sacrificio, valor que nunca se cumple en la realidad pues
la ecuación provee una protección para que se consuman los ánodos
durante más de un año de navegación continuada y con un importante
margen. Para el mismo barco construido en aluminio este valor se
eleva a 16 kilos y si su construcción fuera realizada en acero este
valor trepa hasta unos 25 kilos.
|
La protección
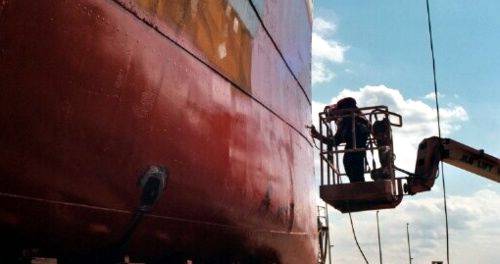
Para los cascos
de acero debemos proteger su superficie mediante una pintura
antioxidante. El barco debe estar bien diseñado en sus fondos y
sentina donde se suele acumular agua, para que se pueda
inspeccionar visualmente y limpiar eliminando las aguas estancadas.
Para evitar la
corrosión electrolítica utilizaremos un cableado con dos conductores
positivo y negativo, y no utilizaremos NUNCA el casco como conductor
de masa para la corriente (como por ejemplo ocurre en la chapa de
los coches).
Debemos evitar
corrientes de fuga especialmente las originadas desde el cable de
corriente del pantalán, mediante disyuntores diferenciales además de
los magneto-térmicos (automáticos) de la instalación de 220 voltios
del barco.
El aluminio y el acero inoxidable
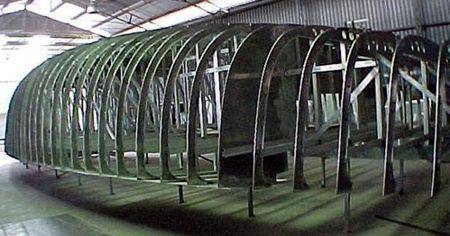
Los dos metales
más usados para los elementos del acastillaje son el aluminio y
acero inoxidable. Existen dos calidades diferentes llamadas Inox-304 e Inox-316. La Calidad 316 es adecuada para ejes propulsores y
elementos que estarán expuestos al agua marina de forma permanente.
En los cascos de
acero, todas las fijaciones al casco de elementos construidos en acero inoxidable deben ser realizadas por medio de soldadura.
Cuando el acero inox se ha calentado entre los 600º C y 900º C
durante la soldadura, precipita en la superficie un carburo de cromo
que si no es eliminado por medio de ácido y de un fino pulido
acabará oxidándose al entrar en contacto con agua salada.
La colocación de
los accesorios de aluminio debe protegerse ya que este material
aparece como cediendo masa por ser menos noble que el acero en la
escala galvánica. Debemos utilizar adhesivos selladores y aisladores
de calidad para todas las superficies en que estos elementos.
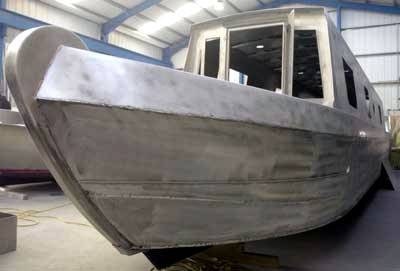
¿Si el aluminio
es tan poco noble, porqué no se oxida? El aluminio produce en su
oxidación una película exterior de oxido de aluminio, que a
diferencia del óxido de hierro es totalmente insoluble en agua y
extremadamente dura. De hecho los zafiros o el rubí no son más una
cristalización del óxido de aluminio.
Es justamente
esta delgada capa de óxido la que protege al aluminio. El aluminio
pulido es tan brillante como un espejo, y los mejores espejos están
fabricados mediante una delgada capa de aluminio. El óxido de
aluminio tiene ese característico color gris aluminio, que es el que
vemos en los palos de los veleros.
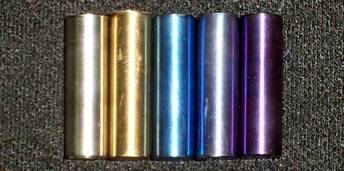
En la fábrica los mástiles son oxidados
mediante un baño ácido y electrolítico para crear esta importante
capa protectora. El proceso llamado anodizado permite cubrir el
aluminio con una capa de solo unas décimas de micra de este duro
óxido conocido también como corindon, y que mediante varios tintes
consigue dar el acabado negro o de colores que vemos en las piezas
tratadas como mosquetones, mordazas, pianos, palos, …
|
Oxidación de la jarcia; corrosión
por tensión y por fatiga
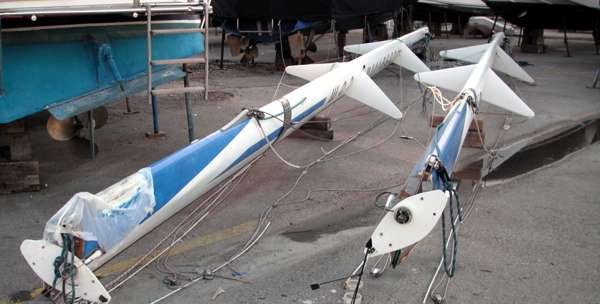
Cuando el acero,
incluso el inoxidable está sometido a excesivas tensiones de
trabajo como ocurre por ejemplo en la jarcia fija, e pueden
producir puntos de concentración de fuerzas donde, se visualizan
zonas con mayor tendencia a iniciar un proceso de corrosión.
La corrosión por
fatiga está causada en áreas o piezas que están sometidas a cargas
alternadas de tracción o compresión lo cual produce la aparición de
grietas o fisuras superficiales que están abiertas a la oxidación.
La misma vibración que provoca el viento sobre la jarcia en puntos
donde además existe mucha tensión mecánica tiende a incrementar la
corrosión por fatiga. También se incrementa en lugares con muy bajas
temperaturas cuando el acero está muy frío y en lugar de deformarse
plásticamente puede volverse quebradizo y agrietarse incrementándose
entonces la corrosión en las grietas.
Artículos relacionados:
-
¿Sabes de ánodos?
-
El antifouling
-
Cuidados en el casco
de fibra
-
Antiincrustantes en la
obra viva
-
Los antifouling más
avanzados
-
Ánodos de sacrificio
-
Renovar un casco en
profundidad
-
Ventajas del aluminio
-
Materiales y cascos oceánicos
-
El caracolillo en el
casco
-
Cuidados y
mantenimiento de las embarcaciones
|