bronce
mezclan además pequeñas cantidades de níquel, fósforo,
manganeso, aluminio, silicio o plomo para conseguir mejorar sus
propiedades mecánicas de forma significativa.
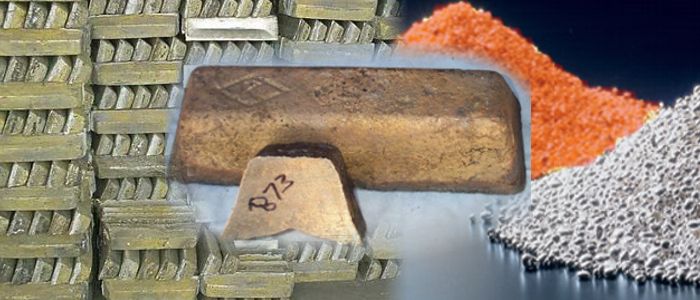
Al añadir
fósforo la aleación conseguida mejora mucho en dureza pero dificulta
los trabajos de fundición. El plomo lo hace más moldeable pero menos
duro. Cuando en vez de estaño se utiliza zinc la aleación de cobre
resultante es conocida como latón, con peores prestaciones,
sobre todo frente a la oxidación, y si además de zinc lleva estaño
entonces la aleación es conocida como latón rojo. El latón se
desintegra rápidamente en entornos salinos lo cual puede tener las
peores consecuencias si lo utilizáramos por error como pasa-cascos y
otros elementos de tuberías bajo la línea de flotación.
La mayoría de
las aleaciones de bronce son muy resistentes a la oxidación en
ambiente marino formándose la típica patena que lo protege de
futuras oxidaciones. Pero esta capa protectora natural no lo
protegerá frente a los procesos electrolíticos y galvánicos por lo
que sigue siendo muy necesario la utilización de ánodos de
sacrificio de zinc que se consumirán antes al tener una escala de
electronegatividad más baja. Algunas marcas de ánodos de sacrificio
comienzan a sustituir el zinc por aleaciones de aluminio
especialmente formuladas para proteger el barco, especialmente
cuando lo tenemos en aguas salobres como las de los estuarios de los
ríos.
Pero durante
miles de años el bronce ha sido utilizado para fabricar armas
blancas y más adelante balas de cañón gracias a su bajo coeficiente
de fricción, así como todo tipo de utensilios y objetos como por
ejemplo las campanas de templos. Las mejores campanas están hechas
de bronce con un 30% de estaño y una pequeña proporción de plata, y
dependiendo de esta aleación y la forma y tamaño de la campana surge
su característica y única sonoridad.
Basta dar una
vuelta por un anticuario para comprobar todo lo que hace algunas
décadas estaba fabricado en bronce en cualquier barco, tanto de
recreo como comercial; bitácoras, cornamusas, herrajes, mosquetones,
brújulas, hélices, y demás artilugios náuticos. El bronce ha sido el
metal rey en ambientes marinos y sigue siendo utilizado en muchas de
las mejores hélices para barcos.
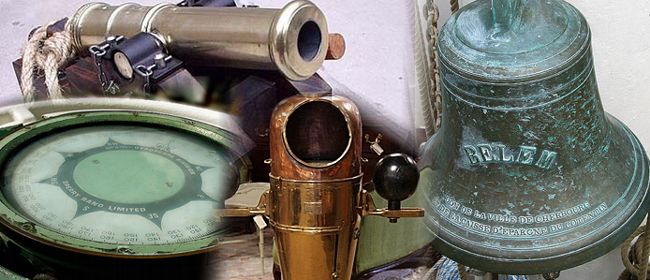
Antes de descubrirse las aleaciones de acero inoxidable, el bronce
era el rey en los barcos clásico.
Tornillería, acastillaje, cornamusas, bitácoras, compases,
campañas... todo se fabricaba en bronce.
El bronce marino de mejores
prestaciones es conocido como Bronce Ab2 y lleva níquel y aluminio o
bien el Htb1 también conocido como bronce al manganeso, siendo estos
dos tipos de bronce más resistentes a la flexión y por tanto a la
rotura y a posibles problemas de picaduras debidos a la cavitación.
El bronce Ab2 pesa además del orden de un 15% menos respecto a
bronce puro de cobre y estaño y es más duro y de mejores
prestaciones mecánicas. Por ello es el mejor tipo de bronce para
conseguir hacer un mecanizado perfecto de las palas en el torno de
trabajo y poder aligerar el grosor de las palas para conseguir las
mejores hélices de bronce.
Es casi
imposible conocer a simple vista la calidad de la aleación de bronce
de que está hecha una hélice y por ello es importante poder confiar
en la reputación del fabricante que en muchos casos formula en
fábrica su propia aleación para conseguir las prestaciones ideales
para su producción. El bronce sigue siendo el material ideal para
producciones de pequeñas tiradas como suele ser el caso en náutica
de recreo.
Cuando las cadenas de producción industriales así lo
permiten por volumen de producción, como es el caso de los motores
fueraborda, el acero inox toma el relevo como material perfecto para
estas hélices. Pero el bronce sigue siendo en cualquier caso un
material más dúctil que el inox, lo cual significa que en caso de
impacto con una roca la pala se doblará en vez de astillarse o
partirse como, ocurre por ejemplo con las hélices realizadas en
aleaciones de aluminio. Además el bronce permite una más fácil reparación.
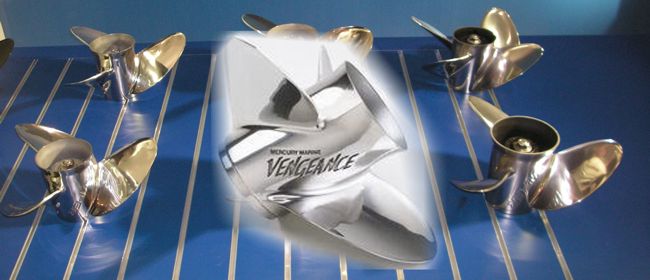
El
Inox es el material perfecto para las grandes tiradas, como ocurre
en los motores fueraborda.
Artículos relacionados:
-
Materiales y Cascos
Oceánicos
-
Ventajas del Aluminio
-
El acero inoxidable
-
Reparar una hélice
dañada
-
Hélices marinas